Welding Technologies
Modular and high-performance solutions to ensure efficiency, precision, and reliability in each application.
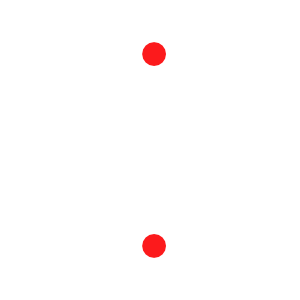
Our welding machines are designed to be flexible and modular, allowing the integration of various technologies and accessories to meet specific production needs.
Through thorough testing and targeted design for maximum reliability, our welding machines guarantee consistent performance over time, reducing downtimes and optimizing the production cycle. Moreover, a wide range of customizable accessories and tools allows for configuring the perfect solution for every industrial requirement.
Why choose us?
Benefits of our solutions
Versatility
With a full range of welding technologies that adapt to multiple materials and applications.
Modular structure
With a full range of welding technologies that adapt to multiple materials and applications.
WELDING
Our machines
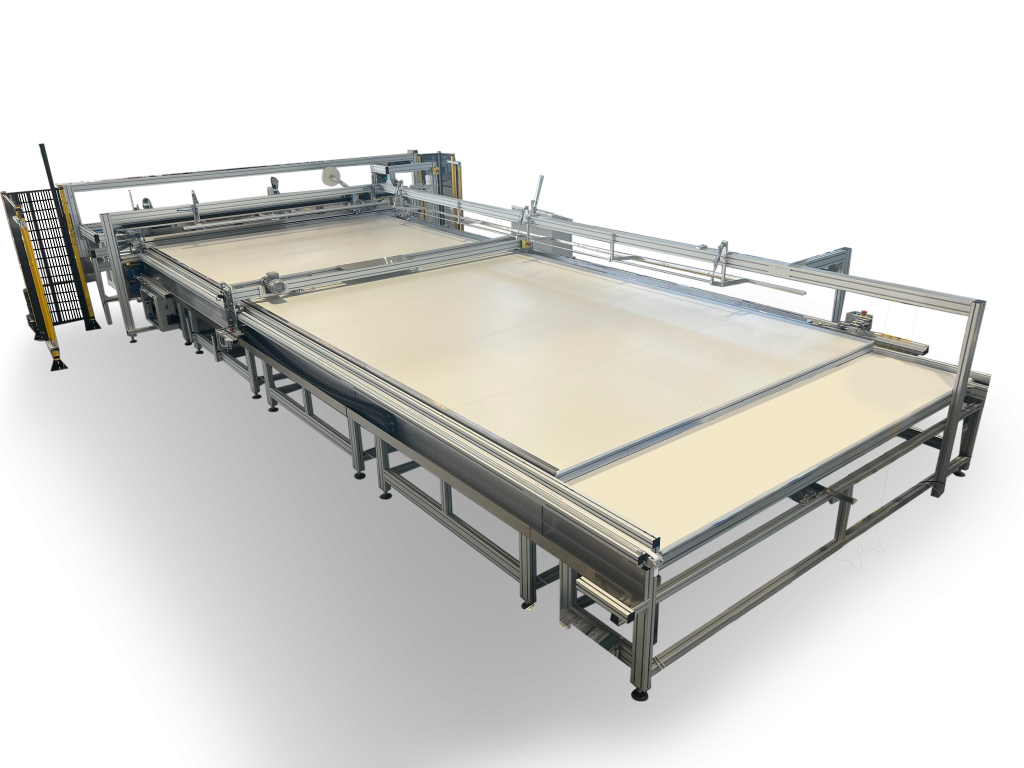
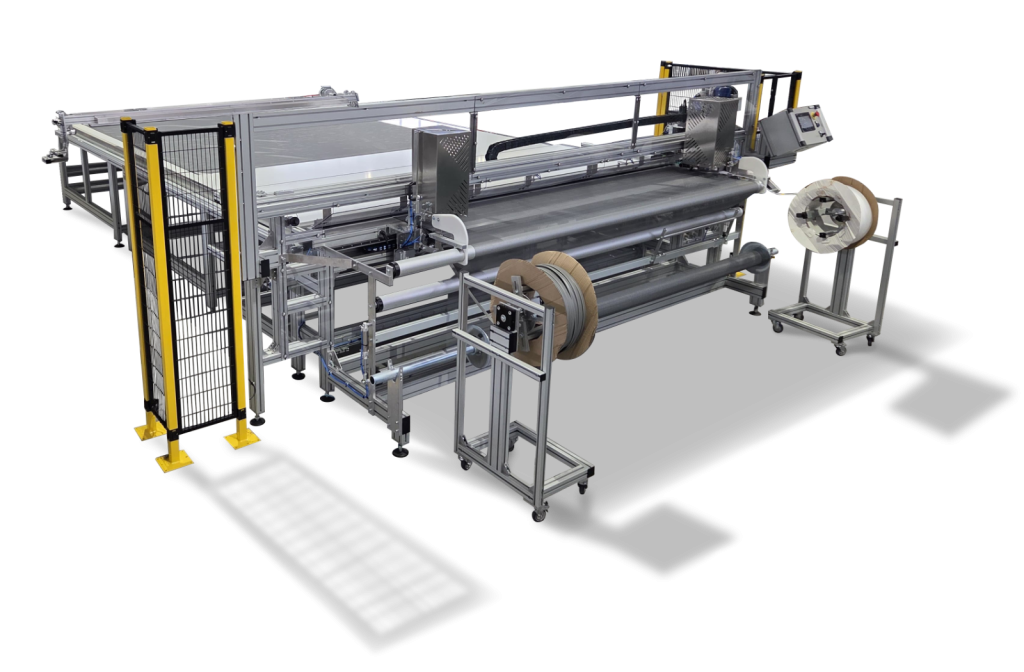
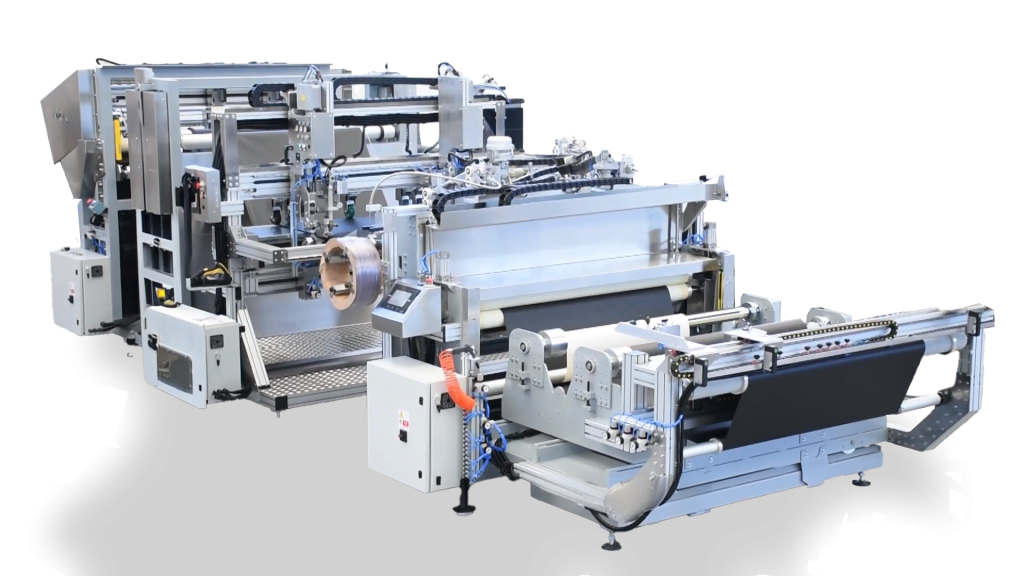

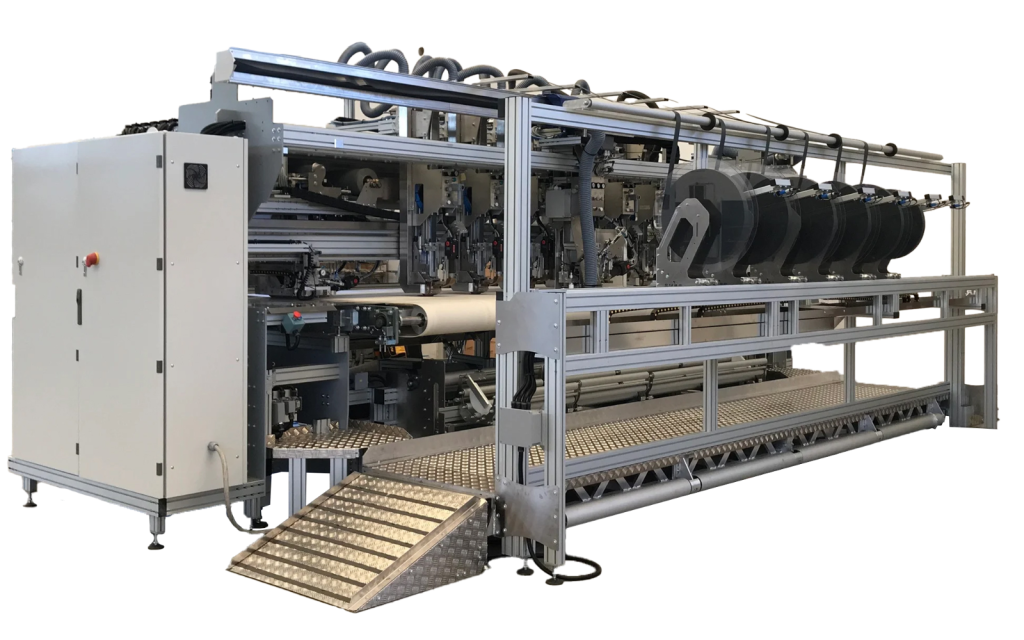
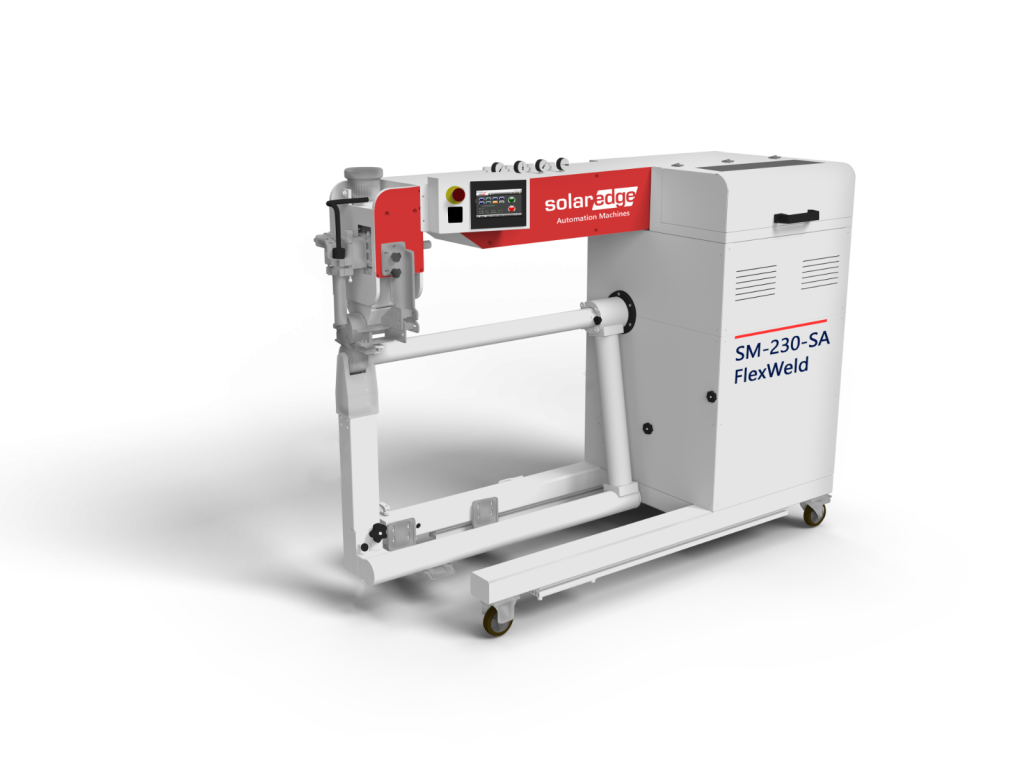
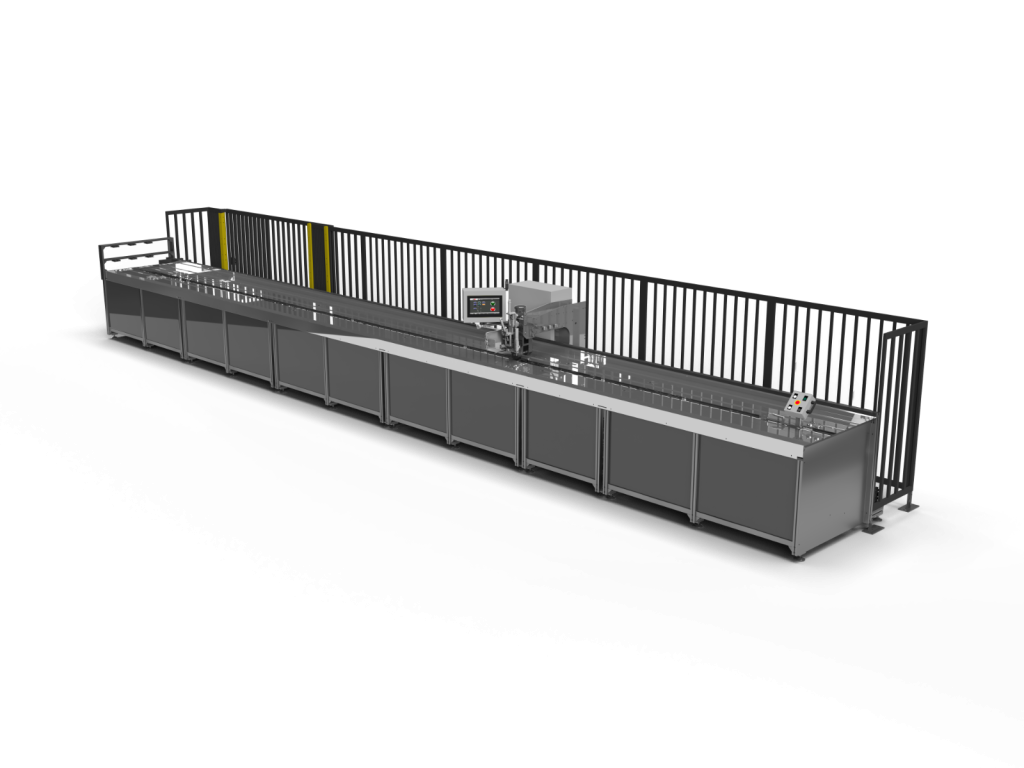
Welding Types
Which is the ideal welding technology for your needs?
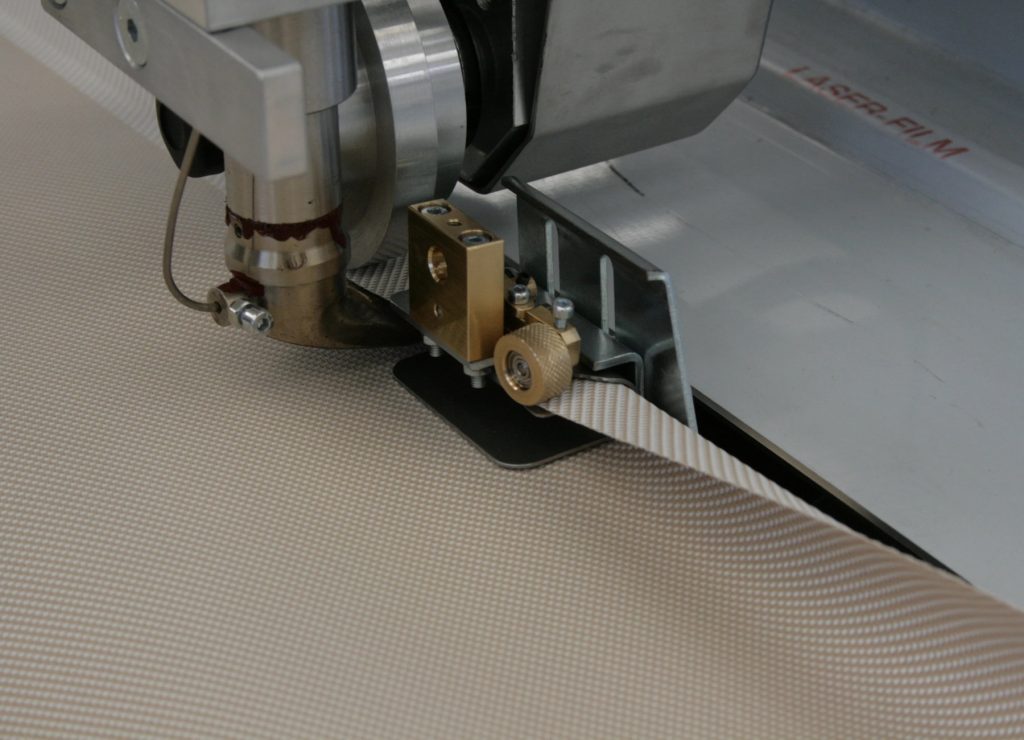
Hot air welding
Our hot air welding machines represent the ideal solution for joining heat-sensitive materials with maximum precision and reliability. Thanks to an advanced heating system, compressed air is brought to a controlled temperature and directed through a nozzle between two layers of material, causing them to melt. Subsequently, high-pressure welding wheels complete the process, creating uniform, aesthetically flawless, and highly durable seams.
This technology is particularly suited for materials such as PVC and thermoplastics, ensuring perfect welds without damaging the surfaces.
Control and Precision
Our machines are designed to offer maximum control over every stage of the process. With digital adjustment of temperature, airflow, and pressure, it’s possible to tailor the welding to various industrial applications.
Intelligent Torque
To ensure flawless welds, we integrate the patented Intelligent Torque technology, which automatically manages the fabric tension during the processing cycle. This system prevents seam wrinkling, ensuring flat, uniform, and durable joints, even on complex materials such as PVC crystal or panels with extruded profiles.
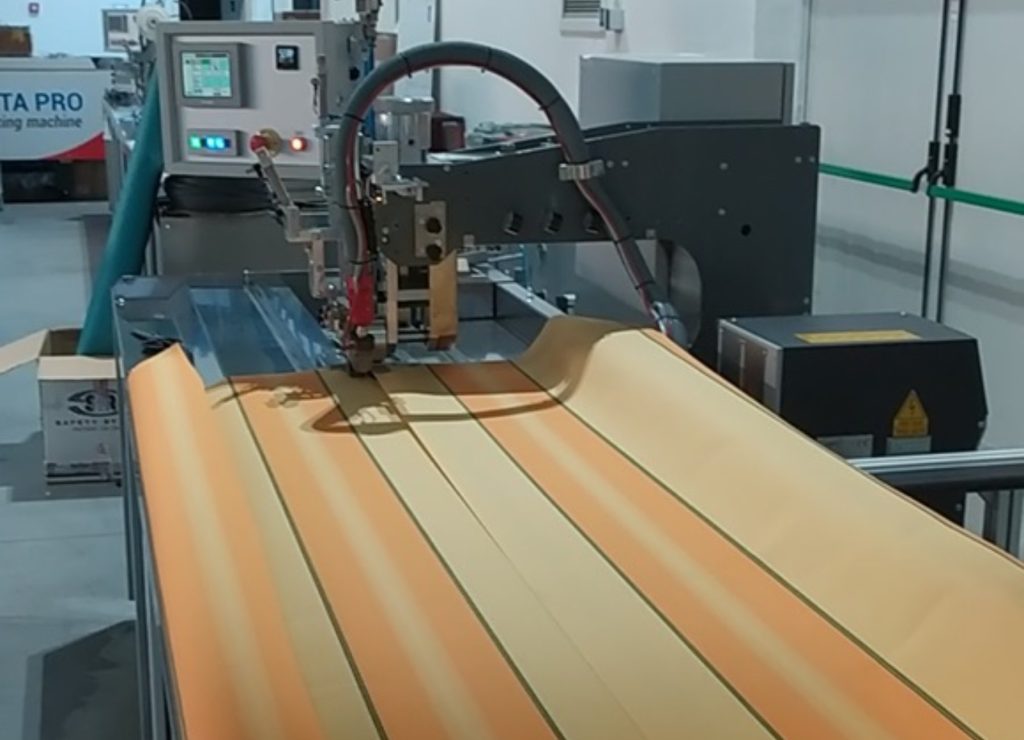
Liquid Glue Welding
Liquid glue welding (hot melt) is an innovative alternative to traditional sewing, ideal for joining technical fabrics such as acrylics and polyesters. In addition to ensuring a strong and durable bond, this technology enhances the aesthetics of the seams and makes them waterproof, preventing fabric perforation. This is the perfect solution for applications requiring long-lasting quality and reliability.
Thanks to the patented Intelligent Torque technology, our welding machines ensure perfectly controlled fabric tension throughout the entire processing cycle, preventing seam wrinkling. This advanced system allows for uniform, precise, and top-quality welds, both in terms of strength and aesthetic finish. With over 25 years of experience in designing and building industrial welders, we offer reliable and cutting-edge solutions to optimize every stage of the production process.
Types of Glue
Cutting Edge welding machines with liquid glue technology can be set to use two types of glue, depending on the materials being processed:
- Nylon adhesive: Used for uncoated fabrics, it ensures a strong and durable bond without compromising flexibility.
- Polyurethane adhesive: Specifically designed for self-cleaning fabrics coated with Teflon, it provides effective adhesion even on difficult-to-treat surfaces.
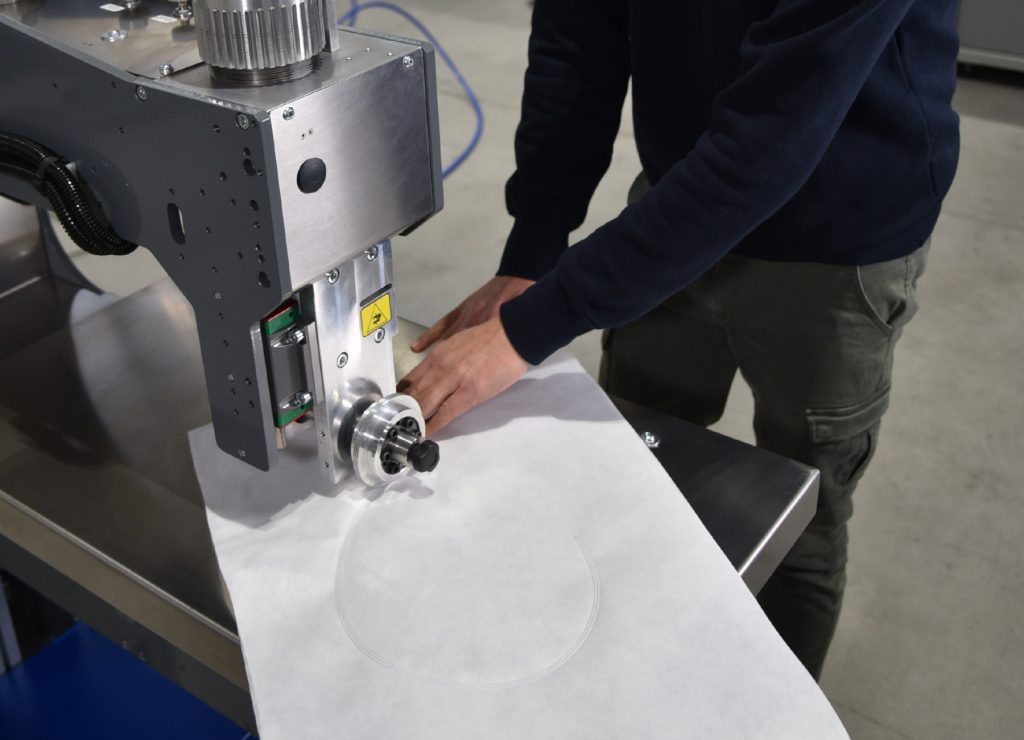
Ultrasonic Welding
Ultrasonic welding is an advanced technology that uses high-frequency vibrations (40 kHz) to quickly and efficiently bond technical fabrics. By converting electrical energy into mechanical movement, the vibrations are applied locally to the heat-sensitive fabric layers, causing the material to melt. Subsequently, welding wheels apply pressure, creating uniform and durable seams.
This method is particularly valued for its ability to create precise welds without using additional materials such as adhesives or threads.
Efficiency and Precision
Ultrasonic welding ensures speed and energy efficiency, with extremely short cycle times, often measured in milliseconds. This helps increase productivity while reducing energy consumption. Additionally, the process guarantees aesthetically flawless seams, with uniformly sealed edges for a professional and flawless result. High quality finished products make this technology ideal for applications requiring precision and long-lasting reliability.
Process Sustainability
This technology offers repeatability and stability, ensuring consistent results even in large-scale production. Once the operational parameters are set, the process minimizes variations between batches, guaranteeing uniformity and optimal performance. Additionally, ultrasonic welding is eco-friendly, as it requires no solvents or additional materials, contributing to a more sustainable production process. Our machines provide advanced control of operational parameters, delivering high-quality seams on a wide range of technical fabrics, backed by over 25 years of experience in the industry.
What you can weld with our machines
Industrial doors
Shade Sails
Tension structures
Advertisement Banners
Composites
Roller blinds
Custom mosquito nets
Inflatables
Awnings
Gazebo
Keder
Truck tarps
Pergolas
Pool covers
Talk to an expert and discover the perfect solution for your company
Fill out the form to send us your request
Contact us on Whatsapp
+39 345 15 33 446
Why choose us?
Online demos
Experience
For more than 25 years, we have been designing and manufacturing machines for industrial production, offering customized solutions for every need.